Electrolytic Machining of Tungsten Needle
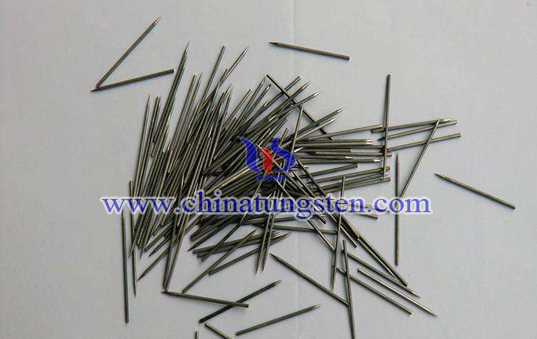
Tungsten needle can be manufactured from the straighten tungsten wire or tungsten rod. One of the method of testing the effects of tungsten needle by electrolytic machining is showed following.
In this study, an electrolytic micro-machining tester is employed to investigate the effects of the supply voltage, the immerse depth of tungsten rod, and the machining time on the current waveform, the material removal rate, and the geometry of the tungsten needle. The tungsten rod to be electrolyzed is dipped in an aqueous electrolyte of 10 wt% sodium hydroxide as the anode, and the stainless steel ring as the cathode. The spindle rotating speed and the stirring rotating speed are set to be 100 rpm and 200rpm, respectively.
According to analyze the topography of the tungsten needle, four machined regimes have been identified as non-machined regime, incomplete machined regime, complete machined regime, over machined regime. In order to obtain the perfect tungsten needle, the experiments are conducted in the complete machined regime. Results show that the tungsten rod becomes a short cone for the immerse depth of 5 mm, and a long cone for the depth of 10mm. When the immerse depth of 10 mm and the supply voltage of 3V, the surface of tungsten needle becomes rough slightly and the tip radius of tungsten needle is about 2gm. With increasing the supply voltage to 4.5 V, the surface of tungsten needle is uniform with a downward trend in material removal rate, and the tip radius can achieve a submicron. For the supply voltage of 6V, because the material removal rate varies violently, it becomes very difficult to control the diameter of tungsten needle.
During the machining time between 0 to 10 min for the supply voltage of 4.5V, the diameter of tungsten rod is decreased from 1000 to 200gm, but during the machining time between 10 to 12.5 min, the tungsten rod gradually transforms into the needle due to a downward trend in current, and the tip radius is decreased from 200gm to submicron. Hence, the machining time must be controlled accurately to manufacture the needle in a submicron radius.(Information from essay)